Plastic extrusion for thermoplastics, PVC, and engineering plastics
Plastic extrusion for thermoplastics, PVC, and engineering plastics
Blog Article
Comprehending the Basics and Applications of Plastic Extrusion in Modern Production
In the world of modern manufacturing, the technique of plastic extrusion plays a critical role - plastic extrusion. This intricate procedure, including the melting and shaping of plastic through specialized passes away, is leveraged throughout numerous industries for the production of diverse products. From automobile components to durable goods product packaging, the applications are huge, and the possibility for sustainability is equally remarkable. Unraveling the basics of this procedure reveals truth versatility and capacity of plastic extrusion.
The Basics of Plastic Extrusion Process
While it may show up facility, the basics of the plastic extrusion process are based on reasonably uncomplicated concepts. It is a manufacturing process in which plastic is thawed and then shaped right into a constant profile with a die. The plastic extrusion process is thoroughly utilized in different markets due to its efficiency, flexibility, and cost-effectiveness.
Different Types of Plastic Extrusion Methods
Building upon the standard understanding of the plastic extrusion process, it is needed to discover the numerous techniques associated with this production approach. Both primary methods are profile extrusion and sheet extrusion. In account extrusion, plastic is melted and created right into a continuous account, commonly utilized to develop pipes, poles, rails, and home window frames. On the other hand, sheet extrusion creates big, level sheets of plastic, which are commonly further processed into products such as food packaging, shower curtains, and auto parts. Each strategy needs specialized equipment and specific control over temperature level and pressure to ensure the plastic maintains its shape during cooling. Recognizing these techniques is key to utilizing plastic extrusion successfully in modern-day production.

The Duty of Plastic Extrusion in the Automotive Market
A frustrating majority of components in modern vehicles are items of the plastic extrusion process. This procedure has transformed the vehicle sector, changing it into a more efficient, cost-effective, and adaptable production industry. Plastic extrusion is mostly used in the manufacturing of numerous car components such as bumpers, grills, door panels, and control panel trim. The process provides an attire, consistent result, enabling manufacturers to create high-volume get rid of fantastic precision and very little waste. The lightness of the extruded plastic parts adds to the overall decrease in automobile weight, improving gas performance. The longevity and resistance of these parts to warm, cold, and effect enhance the durability of vehicles. Therefore, plastic extrusion plays a crucial duty in automobile manufacturing.
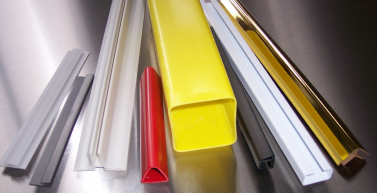
Applications of Plastic Extrusion in Durable Goods Manufacturing
Past its considerable effect on the auto market, plastic extrusion shows equally efficient in the world of customer products manufacturing. This process is important in creating a vast array of products, from food packaging to household appliances, playthings, and even medical devices. The versatility of plastic extrusion allows suppliers to design and create intricate forms and dimensions with high accuracy special info and efficiency. Due to the recyclability of several plastics, extruded elements can be recycled, decreasing waste and expense (plastic extrusion). The adaptability, adaptability, and cost-effectiveness of plastic extrusion make it a recommended choice for lots of durable goods makers, contributing dramatically to the industry's growth and advancement. The environmental implications of this extensive usage need cautious factor to consider, a topic to be reviewed better in the subsequent section.
Environmental Impact and Sustainability in Plastic Extrusion
The pervasive use plastic extrusion in producing invites analysis of its ecological ramifications. As a process that often makes use of non-biodegradable materials, the ecological influence can be substantial. Power consumption, waste production, and carbon emissions are all concerns. Nevertheless, market improvements are increasing sustainability. Reliable machinery minimizes power use, while waste monitoring systems reuse scrap plastic, reducing raw material demands. Furthermore, the development of eco-friendly plastics offers a more eco-friendly option. Regardless of these enhancements, better development is needed to minimize the ecological footprint of plastic extrusion. As culture leans towards sustainability, suppliers need to adapt to stay viable, highlighting the value of continual research and development in this area.
Final thought
In final thought, plastic extrusion plays a crucial duty in contemporary production, specifically in the auto and durable goods fields. Its flexibility permits for the production of a variety of components with high accuracy. Its capacity for recycling and advancement of biodegradable materials uses an encouraging avenue towards lasting practices, consequently addressing environmental concerns. Recognizing the basics of this process is vital to optimizing its advantages and applications.

The plastic extrusion procedure is extensively used in different industries due to Bonuses its cost-effectiveness, efficiency, and adaptability.
Structure upon the fundamental understanding of the plastic extrusion process, it is required to explore the various methods included in this production technique. plastic extrusion. In contrast, Learn More sheet extrusion creates big, level sheets of plastic, which are generally more refined into items such as food product packaging, shower drapes, and auto parts.An overwhelming bulk of components in modern-day vehicles are items of the plastic extrusion process
Report this page